As more DOT specifications call for increased percentages of recycled materials in asphalt hot mix, many still need to be convinced about the performance of pavements paved with RAP and/or RAS. Additionally, there’s confusion over the environmental and financial impact of using recycled materials. These are all valid concerns.
However, using RAP and RAS alone is not the answer. We’ll explore how you CAN achieve better performance, sustainability and cost savings with RAP/RAS hot mixes using a performance grade binder.
Performance
A study by the University of Texas, El Paso (UTEP) evaluated mix designs, design processes and guidelines to identify weaknesses and strengths of balanced mix designs involving RAP, RAS and other additives. According to Soheil Nazarian, Ph.D. — a Civil Engineering Professor at UTEP and the lead researcher on this project — adding more binder enables a more flexible mix that doesn’t crack as easily.
This report by NAPA echoes Dr. Nazarian’s sentiment, stating that “high RAP/RAS mixtures can be designed to have better performance than virgin mixtures when a proper mix design approach (such as the balanced mix design method) is employed.”
We’ve seen many real-world examples in which roads paved with RAP and/or RAS perform the same, if not better, than standard-grade asphalt when a PG binder is added to the mix.
Sustainability
The environmental impact of upcycling pavements and shingles is felt both upstream and downstream in the asphalt supply chain. Using more recycled materials in mix designs not only diverts waste from landfills (up to 34% of landfill space, according to the NAPA report) but also reduces the need to source virgin materials — enabling a pavement lifecycle that is truly regenerative.
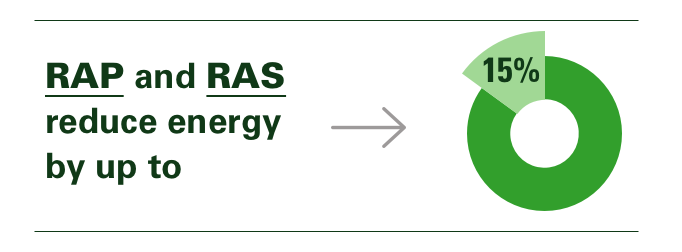
Additionally, that same report claims that RAP and RAS reduce energy by up to 15% — which is key for companies looking to lower their carbon footprint and adhere to EPDs.
At the same time, by engineering roads that last longer, we are naturally reducing the energy and waste materials required to maintain pavements.
Cost Savings
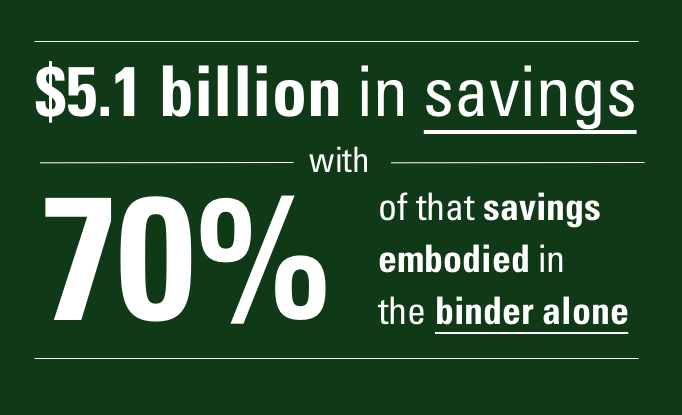
Increased performance and sustainability result in significant cost savings. According to NAPA, the savings from higher binder replacement significantly outweigh the cost of any extra testing that may be required. The total amount of asphalt and aggregate available on an annual basis can result in $5.1 billion in savings, with 70% of that savings embodied in the binder alone.
SigmaBond Checks All the Boxes
Using our SigmaBond modifier as a binder ups the ante for all the key benefits listed here. Because SigmaBond contains completely digested tire rubber, you can pack even more recycled materials into an asphalt hotmix. It’s the only terminal blend PG-TR and ARHM that routinely uses more than 15% RAP. SigmaBond also releases performance-enhancing qualities, such as resistance to cracking and fatigue, low-temperature improvement and reduced discoloration.
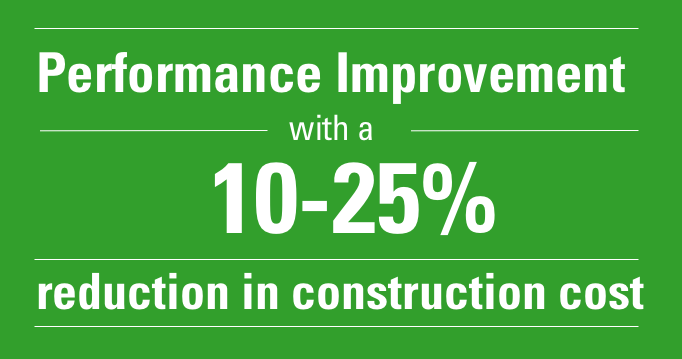
An independent study by the University of Nevada, Reno, correlated this performance improvement with a 10% to 25% reduction in construction cost per lane-kilometer when compared to conventional asphalt pavement. Learn about the science behind SigmaBond here.
We look forward to more studies and discussions around sustainable pavements and hope the asphalt industry continues on the path to reducing waste and building roads that last.
We recently partnered with Texas Materials (formerly TexasBit) to pave city streets in downtown Fort Worth using their multi-purpose asphaltic concrete, MAC Mix. The project resulted in a dense graded ARHM with a smooth, dark finish — but the kicker here is that the asphalt mix included up to 11% RAS and 18% PG-TR thanks to our SigmaBond binder!
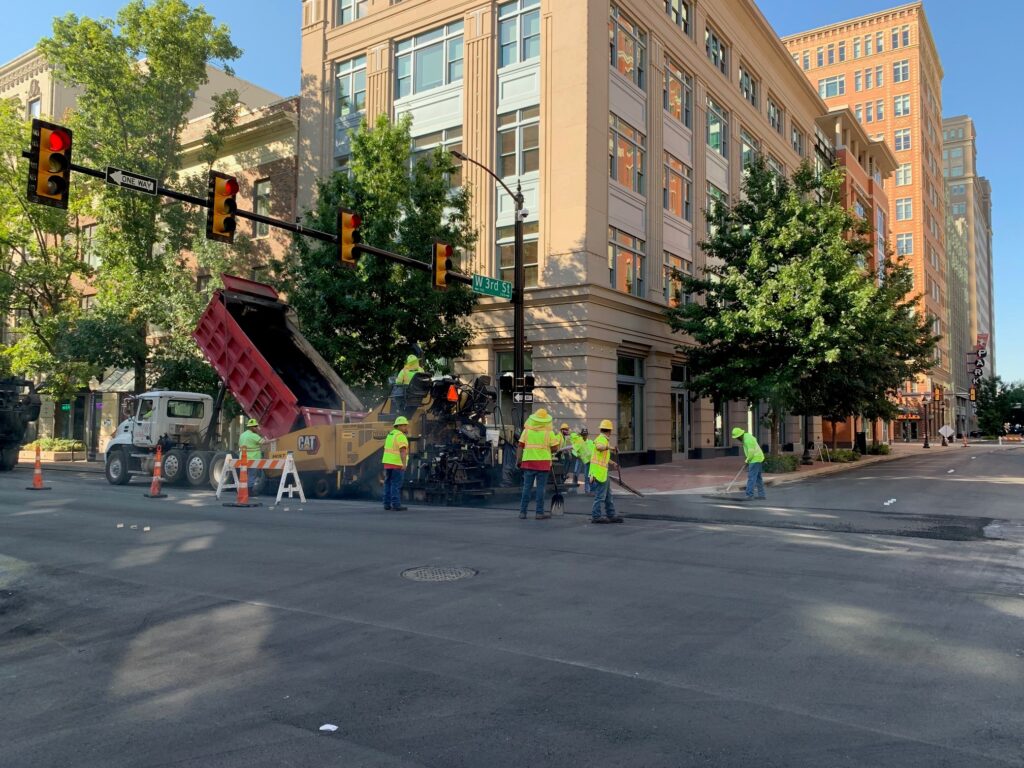
Because SigmaBond contains fully digested tire rubber, its liquid form can seamlessly be added to any asphalt blend (including MAC Mix) without clumping and clogging spray nozzles on the job site. This feature eliminated the need for an additional modifier, enabling the construction crew to complete the project more efficiently. In addition to its superior workability, SigmaBond enhanced the amount of recycled materials that could be put back into the road.
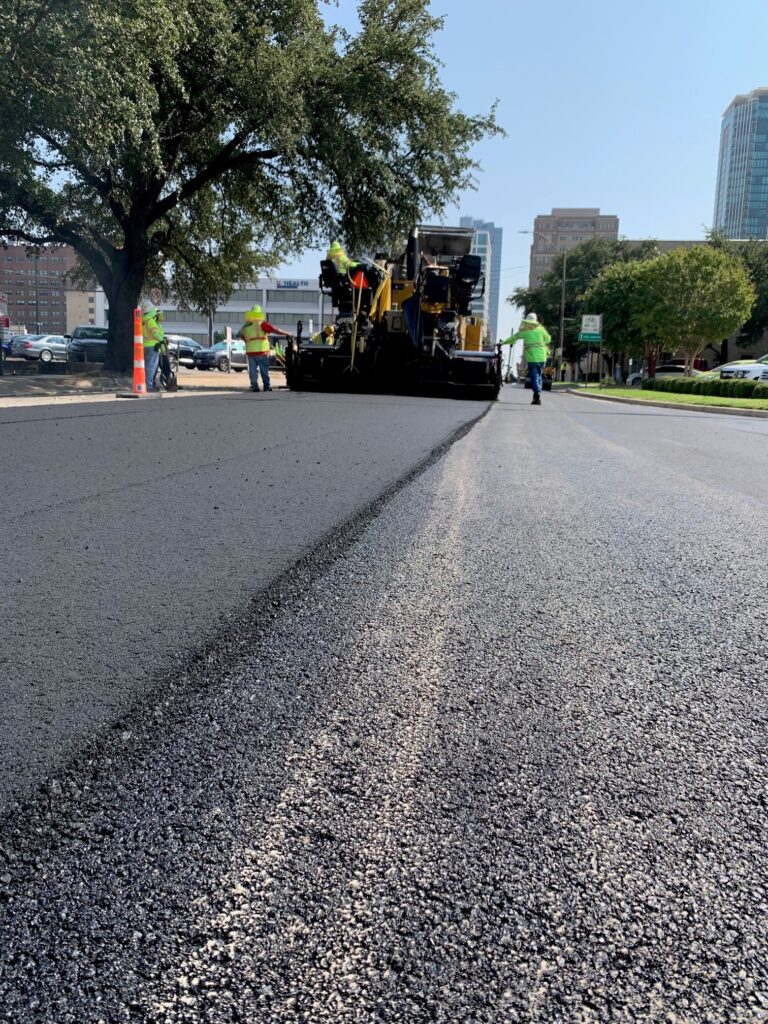
Using SigmaBond enabled Texas Materials to increase the percentage of tire rubber in their mix well past industry standards. This translates into more than 18,000 tires that were diverted from landfills and reused for this paving project alone. Not to mention the recycled asphalt shingles that were repurposed as well. Imagine the impact if all of Fort Worth was paved using MAC Mix with SigmaBond?
While the environmental impact is notable, the performance and long-term benefits of using SigmaBond to enhance a product like MAC Mix is equally important. SigmaBond has consistently proven to strengthen pavements both in the lab and in real world applications, resulting in roads that last longer and that need less maintenance to upkeep. Not only is this a win for cities with heavy traffic but also for taxpayers who are footing the bill.
In Fort Worth, we look forward to seeing how well this pavement holds up and collaborating with Texas Materials again in the future on similar projects. By the looks of this road, it’s already off to a great start!
Polyco’s EHS (Environmental Health and Safety) Manager, Kevin Bush, is a hard worker who cares about his community and doing things right. That’s why he became an Eagle Scout in his youth and why he’s spent over two decades of his professional career dedicated to increasing responsibility in industrial settings. We chatted with Kevin about his life in Texas, how his background in Scouting helps inspire his work, and his vision for the future of recycled materials.
What excites you most about working with Polyco?
Before I worked here, I was with a much larger company — several thousand people strong. It’s hard to change anything there, to make a real difference. Polyco is smaller and newer. You know everybody here, and you can really make an impact in the places that matter. It’s great to be able to help build a company up, to see where it is and help determine where it’s going. On top of that, sustainability is really important to me — to all of us at Polyco, really. I come from a Scouting background. I’m an Eagle Scout; my son’s an Eagle Scout, and we really try to live by the idea of “leave no trace.” Polyco does, too, and that means a lot to me.
What does a normal workday look like for you?
As the Environmental Health and Safety manager, I do a lot with, well, environmental health and safety. I put together training programs, do audits and inspections, and coach our employees, helping them understand the regulations we need to follow and why. On the safety side, the regulations and guidance often make sense as soon as you explain them, but the environmental bits can be a little harder to understand right off the bat.
These days, my team has been doing a lot of reviewing and refreshing Polyco’s policies regarding our environmental and safety programs. We need to ensure everything is in line with state environmental regulations as well as within OSHA standards. Right now, we’re doing a lot to review existing policies and bring them up to date.
What do you think the future holds for Polyco?
The potential for growth we have is exciting, and not just in terms of market share or monetary value. We take things people don’t want — like used tires — and turn what might have just gone into a landfill into raw material for new, high quality roads and roofing materials. I think we’re going to keep doing that, keep growing and keep finding new ways to “leave no trace.”
Attending TXAPA’s Annual Meeting this week inspired us to reflect on our impact in the state.
For almost a decade, our signature asphalt modifier, SigmaBond (which is manufactured right
here in Texas), has improved the longevity of pavements with qualities that enhance
performance across the state’s unique regions. Join us as we explore how SigmaBond builds
better pavements in Texas.
Resists Cracking
While Texas is no stranger to the heat, the harsh climate (coupled with heavy traffic) can take a
toll on pavements if not remedied. Adding SigmaBond to any grade of binder binder is a
proactive way to reduce cracked pavements. Tests run by our R&D lab showed resistance to
thermal and fatigue cracking as more SigmaBond was added to the mix. Additional testing done
at NCAT resulted in no cracking — outperforming other standard grades. Even with the rare
cold snap, SigmaBond has been proven to drastically improve low temperature performance
with increasing percentages of tire rubber in the mix.
Enhances Safety
In both rural and urban environments, road conditions are vital to public safety. Emergency
vehicles can’t afford to be held up by road closures and commuters need smooth, clearly
marked roads to stay in their lanes. SigmaBond protects pavements, keeping them darker and
smoother longer. Additionally, SigmaBond releases the carbon black present in tire rubber to
enhance striping contrast and reduce discoloration.
Improves Sustainability
By enabling hot mix contractors to use more upcycled materials in their mix design, SigmaBond
is contributing to a more sustainable infrastructure. Roads paved with SigmaBond, like this one
near Dallas, outlasted the same grade of asphalt (without SigmaBond) and continues to surpass
performance expectations. With less maintenance needed to upkeep roads, SigmaBond has the
potential to lower construction costs per lane-kilometer by as much as 10% to 25%!
As we reflect on our roots, we’re proud of the paving performance we’ve delivered to Texas for
almost a decade. But, we’re not hanging up our hat yet! Partnerships must be forged between
contractors, terminal operators and TxDOT to raise the bar as an industry. In the meantime, we
will continue innovating sustainable ways to build roads that are Texas tough for decades to
come.
Learn more about the value we bring to Texas paving and the benefits of SigmaBond here.
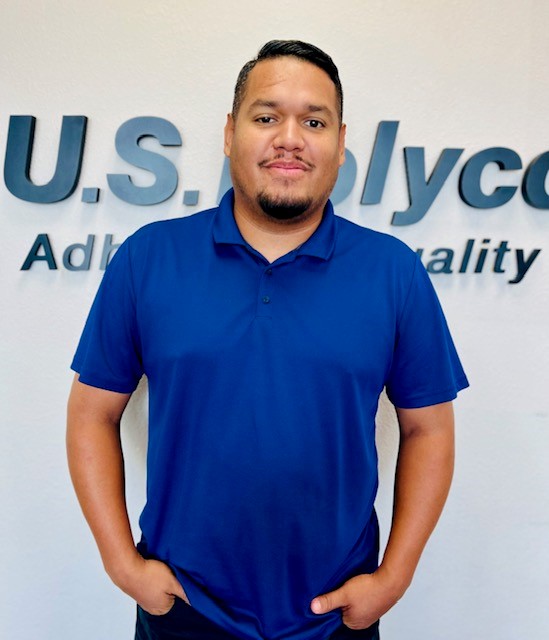
As an Operations Supervisor, Ismael Dominguez’s role is pivotal in the daily operations of the Ennis, TX facility. His responsibilities extend to meticulously crafting plans and procedures that govern the plant’s operations. With a decade of unwavering commitment to Polyco, he’s seen the company evolve and grow, and his journey within it is nothing short of remarkable.
Tell us a little bit about your career with Polyco.
My journey with Polyco started on September 16, 2013. Polyco took a chance on a 24-year-old with little experience in the PMA industry. Since then, I’ve moved up through the company’s ranks to Operations Supervisor of the Ennis plant. I’ve really grown to love operations and have a great team that I can count on.
On a daily basis, I work closely with the Operations Manager, going through operations plans and procedures, as well as planning production schedules weeks to months in advance. We also work closely with the safety team, ensuring safety regulations are followed and everything follows OSHA protocols.
What do you enjoy doing outside of work?
My life outside of the office revolves around my family and sports. I have a competitive spirit, so you can find me playing softball, competing with my wife against ESPN-featured players in cornhole, or leisurely fishing. I guess you can say I’ve passed the competitive gene to my seven-year-old daughter, who’s beginning her journey in tournament ball. If I’m not playing sports, I’m coaching them. Sports have always been, and will always be, a huge part of my life. But family is everything to me. Having them in my corner day in and day out is truly special.
What’s your favorite part about working at Polyco?
What truly excites me about Polyco is the company’s growth. From its humble beginnings, I’ve witnessed Polyco’s remarkable growth on the paving and roofing fronts. Listening to Tom and the leadership team talk about what they wanted to do and now seeing it come to fruition is amazing. It makes you feel like anything is possible, and it is, including employees achieving their desired careers. Having ascended the ranks from assistant operator through safety and back into operations, I’m a testament to the opportunities that Polyco offers its employees. I hope I’m with the company for many, many, many more years.
What’s next at Polyco?
The sky’s the limit. I honestly feel that way, having worked with Polyco for so long. Innovation is something that we really push at Polyco. Coupled with sustainability at the core of Polyco, I see us continuing on that path. Being able to recycle and make a great quality product using trash as our treasure is really important — and cool. I’m just glad I can play a small part in everything Polyco has planned.
Founded in 1994, Polyco entered the asphalt market as a small, family-owned business with big goals. Tom Nichols, our founder, recognized a need for better-engineered roofing and, eventually, paving solutions that embraced a green model of stability. Starting with nothing more than an idea on a napkin, $400, and a company of one, he realized he would have to build a team to achieve these goals.
Being a family-owned business, employees are treated like family and share similar values. To do this, the leadership team at Polyco created an atmosphere of “togetherness” without silos. Tom Nichols, says, “My passion is people and ideas. Those two things are everything to me.” This inclusive approach to business has continued to this day and encourages growing the younger generation within the company to build its future and foster innovation.
John Lopez, a legacy team member, was one of Polyco’s first employees. He reflects on his tenure with the company and its remarkable growth, “I came in as an Operator, sharing many hats as the Plant Manager. The company was growing rapidly, and my career did as well. I became a Lead, then Supervisor, and now most recently moved into R&D. You can do anything you put your mind to at Polyco, and the company encourages it. Now, my son works here and is very happy. I am very proud to be part of Polyco. I love this company.”
Sumer Lucas, Director of Technical Services – Roofing, agreed, “It’s been pretty amazing coming up with Polyco for the last ten years and witnessing the insane amount of growth that’s taking place in the last decade. I’ve had the amazing opportunity to grow and advance with Polyco.”
When asked why she continues to work at Polyco, long-time employee Kaylea LaBee said, “The people. We cherish and rely on each other, creating an environment where we build innovative ideas off one another.”
VP of Marketing and Sales, Sam Nichols, said, “The reason that we’re such an innovative team is that nobody puts as many resources into people, technology, and equipment. This allows us to function differently than most of our competitors.” We do things differently, not just to be different, but because it needs to be better, and when we make things better, good things happen.” Tom adds, “At the core of everything Polyco believes is to make good things happen. A focus on what is possible and why it CAN be done. This leads to a culture of invention and innovation not equaled by our peers.”
With this philosophy, Polyco has led the way in innovation with high-performance, sustainable asphalt solutions for the roofing and paving industry. “To me,” Tom said, “…sustainability is the moral obligation of every citizen.” And as we continue to build the best team in the industry leading the charge, Polyco will continue developing technology that propels sustainability for future generations to come.
For years contractors in California have tried to incorporate used tire rubber into asphalt to extend the life of their roadways but with limited success. Recently, Polyco landed contracts in Northern California to assist with several paving projects powered by our proprietary Rapid Digestion Process™ (RDP), SigmaBond a revolutionary asphalt that enables hot mix contractors to use more upcycled materials while extending the life of pavements. The results have been resounding.
Are you sure this is rubber?
With SigmaBond, contractors had no difficulty with the placement of the mat or rake work. They noted that the product wasn’t sticky, was easy to place, contour and compact, and had density values that exceeded target values. They also reported the tensile strength exceeded regular asphalt – the only time they had seen that happen with a rubber mix. Much to their excitement, we overdelivered what was promised.
Many state contractors still use the dry process which simply adds raw dry tires to the aggregate as a filler. The wet process mixes tire rubber into the process wet at about a 20-25% concentration. The Polyco process digests it into a liquid process allowing more rubber to be added – up to 50%.
Jeffrey Buscheck, R&D Engineering Manager at the UC Pavement Research Center, believes that “the use of TR-modified asphalt as a tool to improve performance in California dense graded mixes is very exciting as we evolve to balanced mix design (BMD) and emphasize on improving the age and crack resistance of our pavements. We are working on evaluation studies funded by Caltrans and CalRecycle, and so far, the results of this material are very promising.”
The positive feedback kept coming as contractors noted that at any stage of the process of laying the material down, the density of compaction did not change. There was none of the stringing that traditional mixes created. They also successfully used our rubber modified asphalt in a dense graded mix which has not been done before with any other rubber mix.
California is admired for its emphasis on sustainability and offers a welcoming environment for Polyco’s products and technology as decision makers want to move away from dry mixes all together. Our SigmaBond process not only creates a superior, long-lasting road without cracking, but it saves money by cutting out the interlayers of traditional roads. Now contractors can meet the state’s sustainability goals without sacrificing performance.
A Note from Polyco: We have enjoyed working with independent asphalt consultant Skip Brown, bringing SigmaBond to Northern California. Read more about why he raves about Polyco’s product to his clients.
My family had an asphalt business for over 70 years, started by my father, so I’ve been in this industry my whole life. I’ve been in the field so long I wore out more than 50 pairs of paving boots! I’ve retired from fieldwork, and now, I consult with clients about the care, maintenance, and proper repair of asphalt pavements.
I first learned about Polyco’s product when I met Bob Rivers last fall. SigmaBond incorporates tire rubber unlike any other asphalt mixture in the market.
Putting rubber in asphalt has two main benefits:
- The rubber helps the asphalt be flexible, preventing cracking longer than non-rubberized asphalt mixtures.
- It offers an alternative to discarding tires, preventing landfills from filling up and reducing toxic fumes from burying or burning scrapped rubber.
Many agencies in California use crumb rubber gap-graded asphalt that has a reduced aggregate structure resulting in a pavement with increased porosity. This type of asphalt works well for California highways as a top layer over dense graded asphalt because it absorbs water and reduces tire-spray. But for roads without adequate structure and cracked dense graded asphalt, absorbed water enters the subgrade resulting in failure of the surface.
My clients need a rubberized dense graded asphalt pavement which will stay flexible longer—reducing cracking and precluding water from entering the subgrade. This is where SigmaBond performs beyond other asphalt solutions. Polyco achieved this by completely digesting recycled tire rubber and asphalt into a homogeneous liquid state using their proprietary Rapid Digestion Process (RDP)—producing SigmaBond.
The proof is in the pavement. Projects paved 5-7 years ago in Southern California that used SigmaBond, still have no cracks reflecting from the underlying cracked pavement.
I’m proud to promote SigmaBond to my clients. Three projects in Northern California have already been awarded that will use SigmaBond—in Granite Bay, Rancho Murieta and Oakdale. With a competitive cost and better performance than other solutions, SigmaBond was a no-brainer for these projects and will be for many more. As I have been known to say, fix the pig; don’t just put lipstick on it. SigmaBond does that.
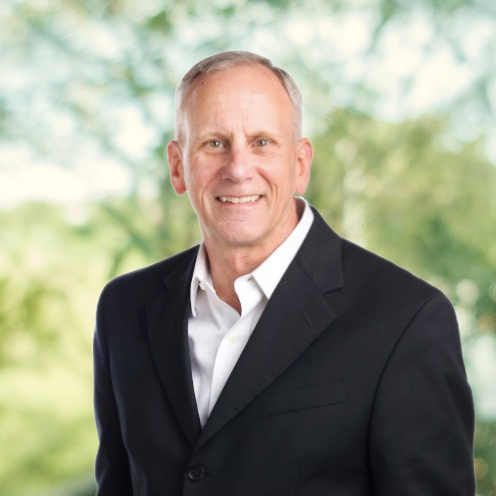
With a degree in Chemical Engineering from Virginia Tech and over 44 years of operations experience, including building a shingle manufacturing plant from the ground up, Tim Machelski was more than qualified to join Polyco as our new Chief Operating Officer. After spending time as a chemical engineer and learning how manufacturing plants and the people operating the plants function, he redirected his focus to operations. Tim looks forward to bringing this extensive experience to Polyco, supporting our team to build on our culture of quality and strong customer relationships. We spoke with Tim about his role and his hopes for the future.
What does the future hold for Polyco?
Before I say something about the future, let me tell you something about the past. My first interaction with Polyco was in 2012, when I went to Tom, the owner, with a need while working for a shingle manufacturer. We wanted to produce polymer-modified asphalt coating that could run at high speeds. Polyco developed a coating that ran smoother, faster, and better than the industry had ever seen. Now, RDP is going to help asphalt become a sustainable product. Polyco is on a growth plan. As we expand, one of my roles will be to keep this company true to its people and roots. I’m excited to help grow Polyco into a world-class organization.
What’s your history with sustainability in the roofing industry?
Under my sponsorship starting in 2012, GAF developed many options for recycling asphalt shingles, leading to the construction of a pilot factory in Lockport, NY, that creates briquettes of recycled asphalt from shingles. This was a considerable undertaking because sustainability wasn’t as big of a priority in 2012 as it is now, and the high price was a hurdle. Nevertheless, sustainability was and still is important to me, so we worked through it and opened the plant. I look forward to further growing Polyco’s—and my own—sustainability record.
What shaped you as a leader?
As a manager at one of the plants, I was approached by a 21-year-old man who had just started and he asked why my attitude was so poor. He said, “You set the culture because you’re the manager.” The next day, I went to HR and asked for a list of every employee. I realized the only ones I knew were the 10% I had to correct constantly. After this, I made it a point to talk to every employee. In fact, at one company, my nickname was “Mr. Rogers” because I warmly greeted everyone each morning. To take this further, I established an Idea Board—no matter who makes the recommendation, it is written on a board and doesn’t come down until it’s implemented or discussed. Respect, fairness, trust, and integrity make up the culture I want to set with my employees.
What do you enjoy outside of work?
I’m very active. I used to run marathons, and now I run for health. I’m also a barefoot waterskier—I can go 41 miles per hour across the water on my bare feet! Working on cars is another passion of mine. Recently, I combined what my faith taught me, “take your graces and share them with others,” with my car hobby and started buying cars, fixing them up then donating the restored vehicles to single mothers.
Focusing on what’s possible is at the core of everything Polyco does. One of the innovations we are most excited about is the technology we’ve developed to reduce landfill waste by recycling waste tires. While there are many ways to recycle tires, Polyco’s patented Rapid Digestion Process (RDP) completely liquefies tire rubber so that it actually improves the performance of the paving bitumen. But don’t just take my word for it!
RDP is the “secret sauce” that powers our revolutionary asphalt modifier, SigmaBond. Two independent studies conducted at the National Center for Asphalt Technology (NCAT) at Auburn University and the University of Nevada, Reno prove that SigmaBond significantly improves fatigue resistance and thermal stability. Ultimately, these features lead to roads that last longer compared to those made with conventional materials.
The NCAT study analyzed several mix designs and evaluated the performance of each one after adding SigmaBond with 20% tire rubber to the mix. The results speak for themselves.
The two formulas with SigmaBond (labeled 82-22SR and 88-22HP) performed better in every category compared to NCAT’s control and unmodified mix design. In fact, the SigmaBond formulation that contained a higher percentage of SBS polymer (88-22HP) actually performed the best — with more than 300 times the fatigue resistance of conventional asphalt.
In the University of Nevada, Reno study, researchers evaluated the crack resistance of tire rubber-modified asphalt mixtures, including SigmaBond. The data shows both SigmaBond samples (PG70-16R and PG70-28TR) with 10% tire rubber significantly increased cycles to fatigue when compared to the PG70-10 conventional asphalt pavement with no tire rubber.
Additionally, the use of SigmaBond was correlated with an overall reduction in fatigue resistance. This performance improvement resulted in a 10% to 25% reduction in construction cost per lane-kilometer when compared to conventional asphalt pavement.
As these studies indicate, SigmaBond outperforms standard paving grade asphalt — enabling hot mix contractors to use more upcycled materials while extending the life of pavements and lowering costs.
The positive impacts on the environment are twofold; not only does Polyco provide a solution to the tire waste stream, but we also develop materials that create more sustainable roads for generations to come.